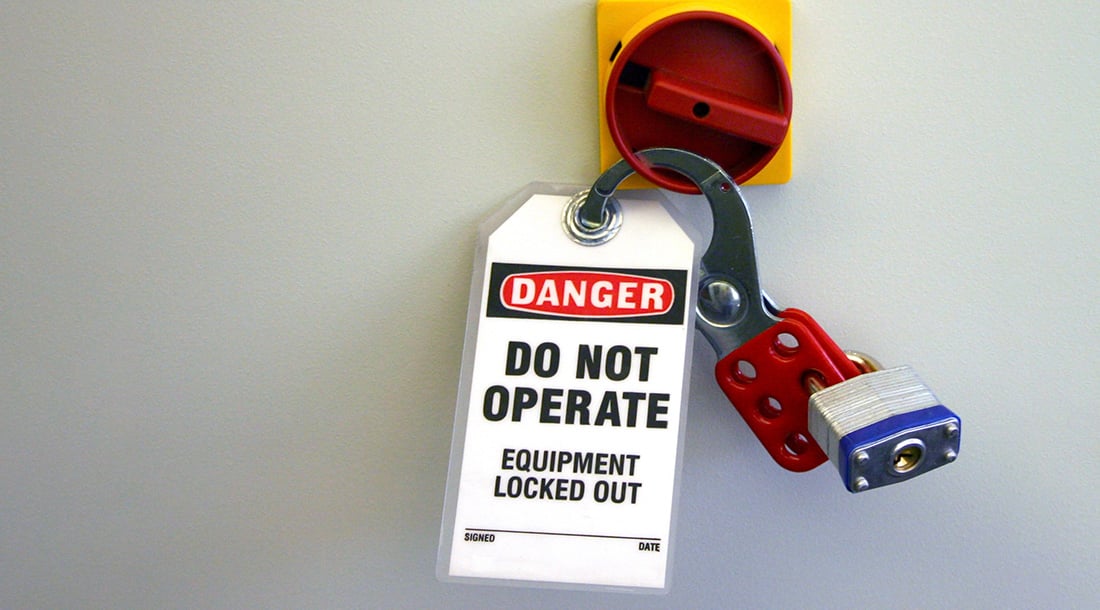
What is Lockout/Tagout and How to Perform It
When it comes to workplace hazards, prevention is always the best defense. And one of the most essential preventative practices across many different industries is lockout/tagout.
Let’s look at what lockout/tagout is, why it’s important, and the basic steps associated with the procedure.
What is Lockout/Tagout?
Lockout/tagout (LOTO) is a procedure designed to protect workers from the release of hazardous energy, specifically the unexpected startup or release of energy from equipment or machinery that is being serviced. According to OSHA, hazardous energy sources include electrical, mechanical, hydraulic, pneumatic, and any other sources that can result in severe injury or death.
While they are used together, lockout and tagout refer to two separate processes. Lockout is the physical isolation of an energy source from the system that uses it. This is commonly done using a LOTO padlock, though other devices may need to be used for more specialized situations, such as when locking out a valve.
Tagout is the process of labeling or tagging the locked-out equipment to signify that work is being done and that it should not be operated. Tagout also helps to convey potential danger associated with the locked-out equipment. Tagout should never happen in place of lockout, nor should it come before lockout.
Why is Lockout/Tagout Important?
The control of hazardous energy is essential for protecting workers against injury or death during repairs or servicing. According to OSHA, compliant LOTO programs help prevent 120 fatalities and 50,000 injuries each year.
Not only is LOTO critical for keeping employees safe, but it’s also regulated by OSHA, meaning that not complying with OSHA’s LOTO regulations can result in significant fines. Therefore, it’s essential to have a well-defined and effective LOTO program for both employee safety and to avoid penalties.
Lockout/Tagout Steps
The lockout/tagout process can vary slightly depending on the type of equipment or machinery that is being locked and tagged. That said, all LOTO procedures contain the same general steps, all of which are required to keep workers safe and comply with OSHA standards.
Please note: It’s required that all employees that may need to perform LOTO are trained on the procedure – if you haven’t been formally trained on LOTO procedures and/or are not authorized to lockout machinery or equipment, do not perform these steps and reach out to your safety supervisor or a manager.
1. Preparation
When a situation arises that requires LOTO, assess what hazardous energy sources need to be de-energized during the LOTO process, and ensure that all required materials to complete the procedure are available.
2. Communication
Communication should go hand-in-hand with preparation. All affected employees should be notified that the machine or equipment is being shut down and that LOTO is to be performed.
3. Isolation
At this point, the machine or equipment being locked out should be isolated from all sources of energy. This is done via an energy-isolating device, which is designed to physically prevent the transmission or release of energy. Examples of energy-isolation devices include a manually operated electrical circuit breaker, a line valve, or a disconnect switch.
It should be noted that, per OSHA, push buttons, selector switches, and other control-circuit-type devices are not considered energy-isolating devices.
4. Lockout
At this point, it’s time to begin what gives the procedure its name. Attach the necessary lockout device (often a padlock) to all energy-isolating devices. This will keep the energy-isolating device in the “safe” or “off” position.
5. Tagout
Once the device has been locked out, securely tag each device to indicate that LOTO was performed, and that energy should not be restored to the machine or equipment. Tags should also include the name of the person that completed LOTO, their contact information, the date and time, and the reason for the lockout.
6. Verification (stored energy check)
Despite the machine or equipment being locked out, the risk of energy release is not completely eliminated. It’s necessary to check for stored or residual energy and subsequently relieve or deplete any energy that is detected.
7. Confirmation
The last step in the process is to double-check the process. Ensure the area is clear, and then test that the machine or equipment has been isolated by attempting to operate it. Once isolation is confirmed, return all controls, switches, or buttons to the “off” position.
At this point, the machine or equipment is ready to be serviced.
Improve Safety with Crescent
Lockout/tagout procedures are a hallmark of many workplace safety programs and help to keep thousands of workers safe each year. To ensure your lockout/tagout program is current and compliant, it’s best to review your procedure yearly and following along with any OSHA updates in regard to hazardous energy.
At Crescent Electric, we take pride in offering our customers products and services that help them and their employees get home safe each day. Head over to our safety and security page for more information on how we can help!