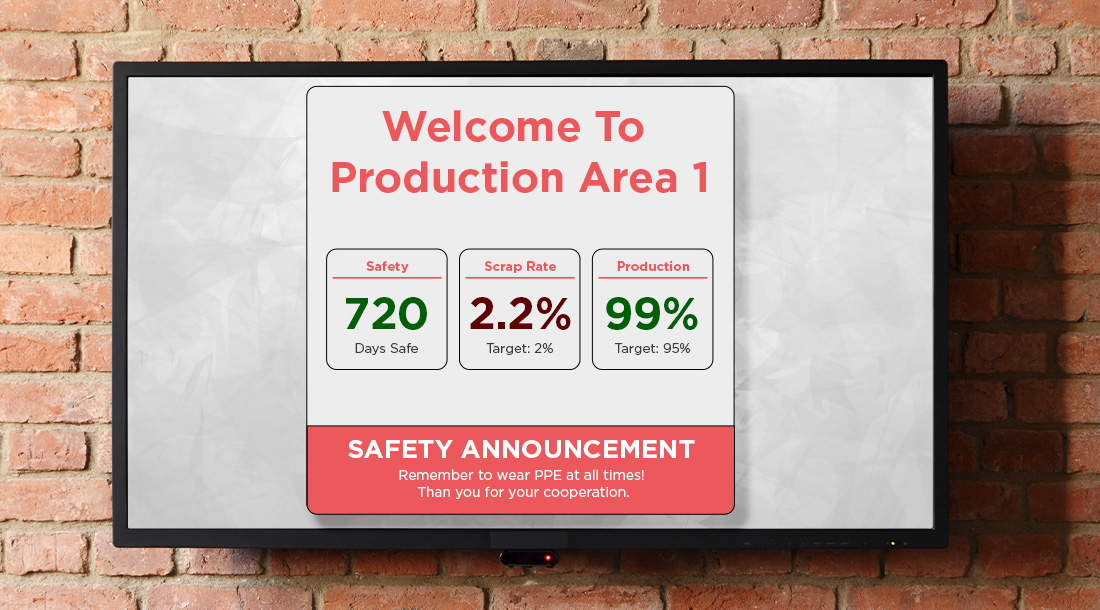
6 Manufacturing KPIs Used to Improve Productivity
Key Performance Indicators (KPIs) are essential for monitoring the health and success of your business. For manufacturers, KPIs also play a critical role in monitoring productivity and diagnosing where improvements can be made.
There are dozens of relevant manufacturing KPIs to monitor, but identifying those most important to your operations can help focus your efforts on the most impactful areas of your business. We’ll take you through some of the top manufacturing KPIs that impact productivity and how to use them effectively. But first, let’s define what manufacturing KPIs are.
What are Manufacturing KPIs?
Manufacturing KPIs are critical metrics that quantify performance and productivity. There are many KPIs that manufacturers can use to improve their operations – from production to delivery. Understanding how to properly utilize manufacturing KPIs is a major factor in improving productivity, lowering costs, and fulfilling your customers’ needs.
6 Manufacturing KPIs Used to Improve Productivity
There are many manufacturing KPIs that measure productivity in some form. Let’s take a look at a few of the most important productivity-focused KPIs that apply to most manufacturers.
Production Downtime
Calculation: Sum of Total Downtime in a Specific Period
Many manufacturing KPIs can be improved by minimizing downtime. Therefore, it’s especially important for manufacturers to track the amount of downtime occurring at your plant.
The cost of downtime in manufacturing is significant — as much as $50 billon industry-wide. Utilizing the Production Downtime KPI can help inform decisions on how to reduce future downtime and improve the productivity and profitability of your facility.
Production Downtime includes both planned and unplanned downtime. Be sure to keep detailed logs of when and why downtime occurred to better understand the nature of it and how to solve it.
Overall Equipment Effectiveness (OEE)
Calculation: Performance x Quality x Availability
OEE is one of the most important manufacturing KPIs for measuring productivity — whether it be across your entire line or a single machine. OEE combines performance, quality, and availability into one metric that can be used to better understand how efficiently your equipment is performing.
These three OEE factors are expressed as percentages in the calculation. These percentages can be used individually as well to determine which factors are performing well and where improvements can be made. The three factors are calculated as followed:
Performance = (Ideal Cycle Time x Total Count) / Run Time
Quality = Good Count / Total Count
Availability = (Planned Production Time – Stop Time) / Planned Production Time
Understanding how to improve OEE is one of the best ways to improve the overall efficiency and productivity of your operations.
Total Effective Equipment Performance (TEEP)
Calculation: Performance x Quality x Availability x Utilization
TEEP is a similar KPI to OEE, but it provides additional insight into the total capacity of your operation. Rather than only considering scheduled production time, TEEP measures the productivity of all time, meaning 24 hours per day and 7 days per week.
Like OEE, TEEP takes into account the Six Big Losses, but it also accounts for Schedule Losses.
Therefore, the calculation is nearly identical to OEE but introduces an additional factor: Utilization.
Utilization = Planned Production Time / All Time
Utilization measures the proportion of time that your machines are in use. This component makes TEEP an especially useful tool for better understanding the potential contained within your hidden factory, the untapped capacity of your plant. Tapping into this potential is an effective way to improve productivity without needing to make additional investments, such as purchasing additional machines.
Throughput
Calculation: Units Produced / Time
Throughput may have a more straightforward calculation than other KPIs on this list, but that doesn’t make it any less important for measuring productivity and efficiency. In fact, Throughput is one of the most valuable KPIs for any manufacturer.
Throughput is the rate of units produced over time. This can be calculated for a single machine or an entire line. In addition to indicating overall efficiency and production capability, Throughput can also be an effective way to determine when there are issues on the line — hence why many facilities monitor Throughput in real-time.
Overall Throughput can be increased in various ways, including reducing downtime and minimizing touch points in a cycle. Automation technology is also a great way to increase Throughput.
First Pass Yield (FPY)
Calculation: (Total Items Produced – Defective Items) / Items Produced
Also known as First Time Through (FTT), FPY measures the rate of quality production. FPY indicates the percentage of products manufactured without errors.
A high FPY indicates that your operations are reliable and efficient. In this sense, FPY also works as an indicator of potential issues with a machine or a line. Monitoring decreases in FPY can allow you to quickly diagnose issues and alleviate them — helping you avoid major losses in productivity and profitability.
Revenue Per Employee
Calculation: Total Revenue / Total Number of Employees
Revenue Per Employee is a high-level manufacturing KPI that directly evaluates productivity levels. Often monitored by upper-level management, Revenue Per Employee can indicate the health of the business — the higher the number, the more productive the business.
The best way to effectively utilize Revenue Per Employee is to track over time to indicate whether the business is growing, stagnant, or declining. It can also be used against industry-specific benchmarks or competitor numbers when available to determine how your operations compare to others in your space.
Improve Your Manufacturing KPIs Now
The manufacturing KPIs outlined above are some of the most important metrics for nearly all manufacturers to track. That said, there are many more KPIs that are useful for manufacturers to develop, assess, and achieve goals for their business. Determining the best KPIs for you — based on your market, business strategy, and more — is necessary to get the most out of these metrics.
If you’re looking for a partner that can help you improve your manufacturing KPIs, Crescent is here to help. Our team of industrial experts can help guide you on the pathway to increased productivity and labor savings. From everyday maintenance to process efficiency overhauls, Crescent has the solutions for your business. Visit our industrial services page for more information or contact us to get started today!